Requirements
- Create a BOM for the product to be manufactured.
- Create a BOM version.
Steps
- Open “Bill of Material Version” from the menu.
- Open the entry of an existing BOM version or add a new one.
- Go to the record tab “Components of the BOM & Formula” at the bottom of the page and click
. An overlay window opens up.
- In the field Product, enter part of the name or number of the product you want to add as a component to the BOM and click on the matching result in the drop-down list.
- Pick a Component Type, e.g., Component.
Note: The Co-Product is a joint product from the production of the main product and can subsequently be added to stock as a finished product itself.
- In the field Qty, enter a quantity.
To record the quantity as a percentage, tick the checkbox Is % and enter the amount in the field % Qty that then appears. (The Qty field is consequently hidden and deactivated.)
Note: A BOM contains the specifications for a single finished product. When the BOM is used, the quantity specified here will be multiplied by the quantity ordered in each case.
- In the field % Scrap, enter the percentage that is to be automatically added as scrap to the quantity specified above.
- Pick a UOM (unit of measure) for the component.
Note: If the unit of measurement selected here differs from that of the component product, a UOM conversion must be defined.
- Pick an Issue Method for how to deduct the consumed materials, e.g., Backflush (completion confirmation) or Issue only for what was received.
Note 1: To deduct the quantity of material per BOM component individually, pick “Backflush”.
Note 2: For automatic issuing, i.e. deducting only the quantity of materials actually consumed, pick “Issue only for what was received”.
- Click “Done” to close the overlay window and add the component to the list.
Note: You can add any number of components to a BOM in this way.
Next Steps
Example
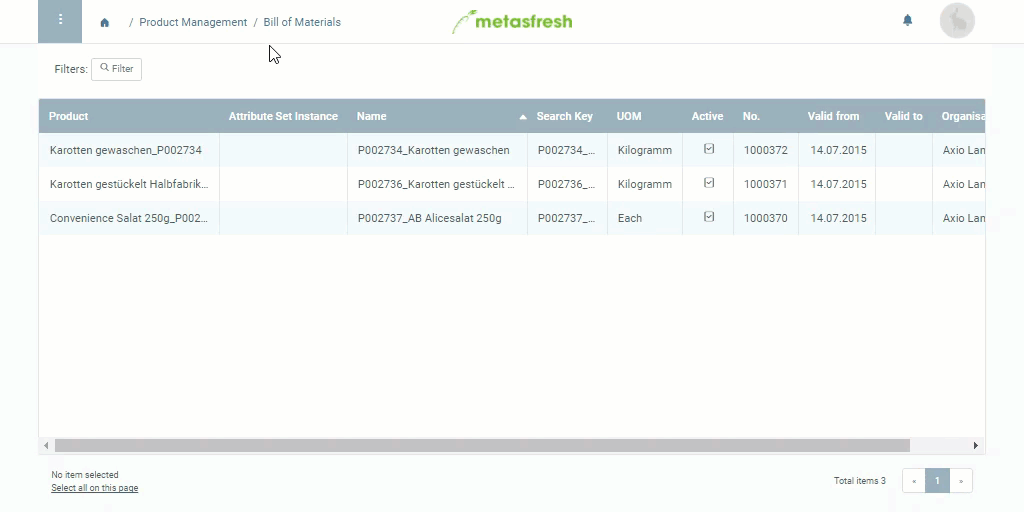
View source file on GitHub.com